Теоретический минимум монтажника. Монтаж электрических проводок систем безопасности. Часть 3
Подготовка трасс электропроводок
Монтаж электропроводок систем безопасности объекта, как и другие виды электромонтажных работ, выполняют в две стадии. На первой стадии осуществляют подготовительные и заготовительные работы. Непосредственно на объекте при определенной готовности строительных работ производят: разметку и подготовку трасс электропроводок; закладку труб в фундаменты и другие строительные основания при переходе из одного помещения в другое и при выходе наружу; осуществляют контроль за установкой строителями или выполняют установку закладных элементов и деталей для последующего крепления к ним оборудования и конструкций: осуществляют контроль за образованием в процессе строительства проемов, ниш, гнезд, борозд, необходимых для установки оборудования и монтажа электропроводок. На второй стадии выполняют собственно электромонтажные работы непосредственно на объекте, В эти работы входят установка на подготовленные места оборудования и электроконструкций, прокладка по подготовительным трассам элементов электропроводок, подключение электропроводок к установленному оборудованию систем безопасности. Строительные работы в помещениях, применяемых под монтаж электрооборудования, в соответствии с требованиями строительных норм и правил (СНиП) должны быть в таком состоянии, которое обеспечивает нормальное и безопасное ведение электромонтажных работ, защиту монтируемого оборудования, кабельных изделий и электроматериалов от влияния атмосферных осадков, грунтовых вод и низких температур, от загрязнения и случайных повреждений при производстве дальнейших работ смежными организациями. До начала работ второй стадии должны быть закончены все строительные и отделочные работы в помещениях, подлежащих оснащению техническими средствами систем безопасности. Установка извещателей, телекамер, пультов управления, считывателей, контрольных панелей, стоек и другого оборудования систем безопасности допускается только после окончательной отделки помещений, окончания монтажа и испытания отопления, вентиляции и других смежных работ Монтаж кабельных линий в траншеях следует выполнять после сдачи заказчику траншей, включая их геодезическую съемку с установлением вертикальных отметок, а монтаж кабельных линий в блочной канализации — после сдачи заказчику блоков и колодцев. Монтаж кабельных линий в кабельных полуэтажах и туннелях производится после окончания побелки и устройства перекрытий. В жилых и культурно - бытовых зданиях монтаж электропроводок производится также в две стадии. Отступления от требований в отношении состояния строительных работ, при которых возможен монтаж оборудования систем безопасности, проводят к порче оборудования и электрических проводок, и на их восстановление, очистку, ревизию непроизводительно затрачиваются средства и труд. Прокладка кабелей в траншеях, не подготовленных полностью к началу укладки кабелей, или по трассам, в пределах которых не выполнены планировочные работы, приводит часто к повреждениям кабелей, особенно при производстве планировочных работ. Подготовка трасс электропроводок состоит из следующих монтажных операций: разметки трасс и мест установки крепежных деталей: пробивных работ для установки крепежных деталей; установки крепежных деталей в строительных конструкциях: бетонных, кирпичных, шлакоблочных и т.д.. Работы по подготовке трасс электропроводок относят к числу наиболее трудоемких операций, особенно при ручном способе их выполнения. 1. Разметка трасс Разметочные работы начинают с привязки трасс к местам расположения аппаратной, пультовой, стояков, кроссировоч-ных шкафов, расширителей, контроллеров, блоков питания, пультов управления, считывателей, телекамер, извещателей и других устройств систем безопасности. Для этого вначале размечают места пробивки отверстий, гнезд и ниш или места установки закладных элементов для закрепления оборудования. Затем определяют и размечают трассу электропроводки, места проходов через стены и перекрытия, места установки коробок, а также места установки крепежных деталей для труб, кабелей и др. Для тросовых электропроводок производят разметку мест анкерных промежуточных креплений, для электропроводок на лотках — мест установки поддерживающих конструкций и точек их крепления к строительным элементам зданий, при прокладке проводов и кабелей в декоративных электрокоробах, по полосам и лентам — мест крепления коробов, полос и лент. При разметке трубных трасс и трасс в декоративных коробах точную привязку мест выхода концов труб и коробов к электроприемникам. Опорные конструкции для прокладки трубопроводов устанавливают в одной плоскости, точно придерживаясь горизонтальных и вертикальных линий разметки. На всей трассе или участке трассы проводки устанавливают две крайние детали крепления и между ними натягивают шнур или стальную проволоку, по которой расставляют остальные детали крепления. В вертикальном направлении разметку производят по отвесу. Определение трасс и мест установки оборудования систем безопасности производят по рабочим чертежам проекта, пользуясь заданными отметками от уровня пола или потолка, расстояниями от колонн, ферм и других строительных элементов, расположенных на одном уровне, или отметками по высоте. Разметку трасс открытых проводок выполняют отбивкой (с помощью окрашенного шнура) вертикальных и горизонтальных линий, соблюдая параллельность линиям сопряжения стен и потолков. Поперечными линиями отмечают места спусков, установки опорных конструкций и крепежных деталей в такой последовательности: сначала у коробок, на поворотах и у проходов, а затем промежуточные крепления. Места установки крепежных деталей, поддерживающих и закрепляющих провода и кабели, располагают вдоль трассы симметрично и на одинаковых расстояниях, не превышающих максимально допустимых по СНиП. Проходы располагают на одной линии и в одной плоскости с прокладываемыми проводами и кабелями. Скрытую прокладку проводов по перекрытиям (в штукатурке, в щелях и пустотах плит или под плитой перекрытия) при возможности выполняют по кратчайшему расстоянию между наиболее удобным местом перехода на потолок (стену) и монтируемым оборудованием. Разметку трасс скрытых проводок, углубленных в борозды стен и потолков, осуществляют по кратчайшему направлению от вводов к оборудованию и приборам. При разметке трасс электропроводок пользуются измерительными линейками, складными метрами и рулетками, разметочными шестами, циркулями, шнурками с отвесами, уровнями и другими специальными приспособлениями и инструментом. Во время разметки трасс электропроводок необходимо убедиться, что в местах установки крепежных конструкций, забивания дюбелей, сверления отверстий и гнезд не будут повреждены уже имеющиеся скрытые электропроводки, отсутствует арматура и не будет нарушена прочность строительных конструкций. Для этого используют специальные приборы для поиска арматуры и скрытых электропроводок. Во всех случаях при разметке и монтаже трасс электропроводок необходимо учитывать удобство монтажа и последующего технического обслуживания монтируемой трассы, а для открытых электропроводок — их эстетическое оформление. Наибольшие расстояния между точками крепления проводок, расстояния между параллельно проложенными проводами, допустимые радиусы изгиба проводов, кабелей и труб, минимальные габариты прокладки проводки над различными поверхностями и другие требования для разметки трасс регламентированы действующими правилами и нормами. 2. Пробивные работы Объем пробивных работ и затраты труда на их выполнение при современных индустриальных методах монтажа резко сокращается благодаря применению прогрессивных способов закрепления деталей и конструкций в строительных основаниях: забивки и пристреливания крепежных деталей; установки закладных частей; образования каналов, борозд, ниш, сквозных отверстий в строительных конструкциях при их изготовлении; приклеивания деталей электропроводок и установочных изделий. Пробивные работы, которых полностью избежать невозможно, должны выполняться механизированным способом. Механизация пробивных работ сокращает затраты труда и обеспечивает правильные геометрические размеры пробиваемых отверстий при минимальном нарушении строительной конструкции. В качестве средств механизации пробивных работ используют электрические и пневматические сверлильные машины и перфораторы, оснащенные рабочим ин- струментом (сверла, буры, шлямбуры, коронки) с пластинами из твердых сплавов, в основном из металлокерамических сплавов ВК (зерна карбида вольфрама, сцементированные металлическим кобальтом), отличающихся твердостью и износостойкостью. Для сверления отверстий и гнезд в строительных основаниях сверлами, армированными пластинами твердых сплавов, полыми коронками и другим рабочим инструментом применяют серийные электрические сверлильные машины, предназначенные для сверления по металлу и дереву. Сверление гнезд и отверстий производят главным образом в кирпичных стенах. Выполнение гнезд в бетоне, даже невысоких марок твердости, не является эффективным. Производительность сверления составляет 10 мм в минуту, а при попадании сверла в твердый наполнитель скорость сверления резко снижается и происходит сильный нагрев, быстрый износ и выкрашивание твердосплавных пластинок, Для сверления отверстий в железобетоне эффективны электросверлильные машины с ударно - поворотными насадками и электромолотки с ударно - вращательным действием инструмента (перфораторы). При использовании этих механизмов для сверления условия работы лучше, и производительность по сравнению с простым вращением сверла выше благодаря более эффективному удалению буровой мелочи и меньшим усилиям, требуемым для удержания инструмента в руках. Для пробивки отверстий больших размеров, особенно в бетонных основаниях, используют сжатый воздух как источник энергии, применяя молотки ударного и ударно - поворотного действия (перфораторы). Пневматический инструмент отличается легкостью, простотой конструкции, надежностью и относительной безопасностью. Поэтому при наличии на строительстве сети сжатого воздуха рекомендуется применять для пробивных работ пневмоинстру-мент. Отверстия в кирпичных и бетонных основаниях под распорные дюбели пробивают механизированным способом. 3. Крепежные работы Крепление монтажных деталей и изделий или элементов электроустановки к строительным основаниям осуществляется путем забивки крепежных дюбелей пистолетом, ручной и пиротехнической оправками, вмазкой в заранее подготовленное отверстие, сваркой к закладным частям, приклеиванием. Выбор способа крепления, если он не предусмотрен проектом, производят в зависимости от вида строительного основания, характера нагрузки, массы закрепляемой детали, а также с учетом трудоемкости и стоимости работ. Забивка в строительные основания крепежных дюбелей Дюбеля надежно закрепляют изделия в строительных конструкциях. Применение дюбелей ускоряет монтаж и облегчает труд монтажников, так как исключаются пробивные работы. Дюбеля делят на три группы: распорные для безвмазочного крепления в предварительно подготовленные отверстия (металлические и пластмассовые); выстреливаемые строительно-монтажным пистолетом; забиваемые ручной и пиротехнической оправкой. Самозакрепляющиеся распорные дюбеля используют для крепления без вмазки в кирпичные и бетонные основания различных электроустановочных изделий и деталей, применяемых при монтаже осветительных и силовых установок. Распорные дюбеля выпускают с конической распорной гайкой. Такой дюбель состоит из корпуса, который представляет собой штампованную или точеную (для болтов диаметром более 6 мм) стальную гильзу из мягкой стали толщиной 8 мм, распорной конической гайки, винта по металлу (с полукруглой, цилиндрической или шестигранной головкой) или болта, двух шайб — нормальной и пружинной. Зубцы на гильзе со стороны закрепляемой детали, а также выемки на гильзе со стороны гайки и соответствующие этим выемкам ребра на гайке препятствуют вращению гильзы или гайки при ввинчивании винта. Гильза имеет два продольных разреза для более легкого ее распирания гайкой при затяжке; для этой же цели конец гильзы со стороны гайки выполнен с небольшим расширением. Дюбеля с конической распорной гайкой применяют для закрепления легких конструкций, небольших щитков, пусковых аппаратов и т.п. Винт и дюбель соединяют с деталью, подлежащей закреплению (скобой, лапкой, ящиком). Затем корпус дюбеля вставляют в подготовленное отверстие распорной гайкой внутрь и легким ударом молотка забивают так, чтобы наружный торец корпуса дюбеля находился в одной плоскости с краями отверстия. Дюбель должен входить в отверстие с небольшим трением. Винт или болт, пропущенный через отверстие закрепляемого изделия, ввертывают в распорную гайку до отказа. При ввинчивании винта распорная гайка, перемещаясь в корпусе дюбеля, распирает своим конусом лепестки корпуса и плотно прижимается к стенкам отверстия, благодаря чему изделие надежно закрепляется. Наряду с металлическими применяют дюбеля из пластмассы и капрона (рис. 7.1). Пластмассовый дюбель имеет цилиндрическую форму с внутренним конусным каналом, корпус его разделен на две половины продольной щелью для облегчения расклинивания. Расположенные по длине наружной поверхности дюбеля ребра уплотняют его в гнезде, улучшают сцепление с поверхностью гнезда и препятствуют проворачиванию дюбеля при ввертывании шурупов. Пластмассовые дюбеля обладают преимуществами по сравнению с другими дюбелями: устойчивостью к динамическим нагрузкам и вибрациям, высокой устойчивостью против коррозии, возможностью применения во влажных и химически активных средах. Для закрепления скоб, установочных изделий и небольших конструкций используют дюбеля с шурупами, а для закрепления поддерживающих кабельных, троллейных и других конструкций, тросовых проводок, аппаратов, струнных подвесок — дюбеля с глухарями. В настоящее время пластмассовые дюбеля полностью вытесняют металлические. Гнезда для больших дюбелей (диаметром свыше 10 мм) пробивают электромолотком и электросверлильной машиной с насадкой, а для дюбелей диаметром до 8 мм сверлят или пробивают ручным пробойником. Выбор размера гнезда, а также закрепление пластмассового дюбеля в гнезде и детали к дюбелю производится так же, как и для металлических дюбелей. Установка крепежных деталей ранее производилась в две операции: сверление или пробивка отверстий и заделка в готовое отверстие крепежной детали. Выполнение креплений за одну операцию стало возможным только после применения в электромонтажном производстве строительно-монтажного пистолета, а также ручной и пиротехнической оправок для забивки стальных дюбелей.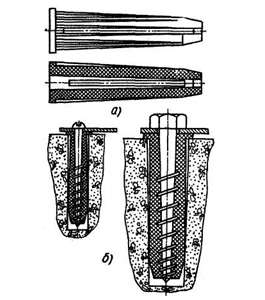
Рис.7.1: Пластмассовые распорные дюбеля: а - общий вид, б - установленные, в - строительное основание
Крепление монтажных деталей и легких конструкций (массой не более 5 кг) к строительным основаниям невысокой твердости производится забивкой крепежных дюбелей вручную. В качестве инструмента для забивки дюбелей в кирпичные и бетонные основания применяют ручную оправку ОД-6, которая представляет собой несложное направляющее устройство, обеспечивающее при забивке дюбеля передачу удара молотка в осевом направлении. С помощью оправки закрепляют трубы, ответвительные коробки, защищенные провода и кабели, шины заземления, профильные монтажные рейки, защитные кожухи и другие изделия, создающие небольшие нагрузки на забиваемые дюбеля. Разметку мест вбивания дюбелей следует выполнять точно и тщательно, так как в дальнейшем исправить неточно забитый дюбель невозможно. В стальных полосах сети заземления и вспомогательных деталях для их прокладки необходимо в местах крепления предварительно просверлить отверстия диаметром 4 мм. Ручная оправка наряду с преимуществами (простота устройства, безопасность и удобство в работе, достаточно высокая прочность закрепления) имеет и ряд недостатков: необходимость нанесения слабых ударов для возврата бойка и добивания дюбеля до упора в деталь после снятия оправки, относительно быстрое срабатывание зажимных губок и, как следствие, ухудшение фиксации дюбеля. Размеры дюбеля выбирают в зависимости от твердости основания и наличия на нем штукатурки: для бетона и железобетона марки 200 и ниже — 25 мм, для красного и силикатного кирпича — 35 мм и для оштукатуренных оснований при недостаточной длине дюбеля (3,5 х 35 мм) — 4,5 х 40 мм. Для проверки правильности выбора длины дюбелей (поскольку качество материала основания, от которого зависит длина заглубляемой части, может оцениваться только приближенно) необходимо по месту работ провести пробную забивку нескольких дюбелей. Правильность выбора длины дюбелей определяется ходом самой забивки, а также прочностью закрепления их в основании. Последнее может быть проверено вытаскиванием дюбеля из основания вручную при помощи плоскогубцев. При забивке в оштукатуренную кирпичную стену возможно попадание дюбеля в швы между кирпичами, что легко обнаруживается отсутствием сопротивления основания при забивании. В этом случае следует дюбель вытащить и заменить более длинным или переменить место крепления. Забивка дюбелей пистолетом или пиротехнической оправкой более производительна, чем ручной. Особенно облегчается забивка дюбелей в бетонные основания. Заделка в строительные основания крепежных деталей путем вмазки Этот способ крепления, являющийся трудоемким, применяется редко, например, тогда, когда упущены закладные части или не могут быть использованы дюбеля для крепления тяжелого оборудования. Вмазка конструкций, штырей и других крепежных деталей состоит из следующих операций:- выполнения в строительном основании гнезда путем сверления или пробивки;
- очистки гнезда и смачивания его водой;
- заполнения гнезда на одну треть или половину цементным или алебастровым раствором (цементный раствор состоит из одной части цемента марки 400 и трех частей песка);
- заделки опорной детали в гнездо.
- металлическими скобами непосредственно к основанию (рис. 2, а);
- металлическими полосками с пряжками непосредственно к основанию или пластинкам из листовой стали, к которым приварены точечной сваркой полоски;
- бандажными металлическими полосками или поливинилхлоридной лентой с кнопками к закрепленным к основанию полосам, лентам и струнам;
- бандажными полосками к специальным держателям, приклеенным к основанию;
- пластмассовыми скобами (рис. 2, б).
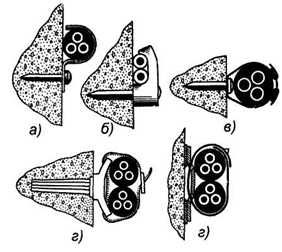
Рис.2: Способы крепления кабелей и проводов: а — металлической скобкой, б- пластмассовой скобкой, в - металлической полоской с пряжкой, г - зубчатой полоской с пряжкой, а - перфорированной лентой с кнопкой (к держателю, приклеенному к основанию)
Рис. 3: Закреп для бандажных полосок: а - общий вид, б - установка закрепа, в - крепление проводов
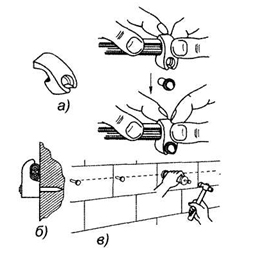
Рис. 4. Пластмассовые скобки: а - общий вид, б - установка скобок, в - крепление провода.
Рис. 5. Крепление кабелей: а - к стальной полосе, б - к стальной проволоке
- расстояния между точками крепления полосы — 0,8-1 м;
- расстояние от концов - отрезков полосы до крайних точек ее крепления — 50 -70 мм;
- разрывы между концами соседних полос—до 300 мм.
Комментарии ()